Rubber crumb surfacing, what actually is it?….
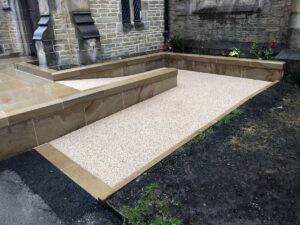
Rubber crumb surfacing is recycled rubber from tires or pigmented rubber. It is mixed with resin and combination to create an aesthetically pleasing alternative to traditional paving. The rubber crumb and resin binder allow flexibility and cushioning. This makes resin-bound surfaces ideal for playgrounds, paths, driveways, and patios.
Have you ever wondered, how to use rubber crumb resin bound on your project? With some simple steps, you can create a unique, sustainable surface. The rubber crumb surfacing provides shock absorption and slip resistance. The resin binder locks the mixture together. The result is an attractive, durable surface.
Rubber crumb surfaces have many benefits . They are permeable, allowing water to drain through. The rubber granules provide a slip-resistant texture. The flexibility reduces stress on joints. With correct installation, these surfaces can last for over 20 years. Creating one is less complicated than you might imagine.
Key information.
Rubber crumb surfaces consist of recycled rubber tire crumb granules used in the base course and pigmented rubber for the top course, bound collectively with a polyurethane glue. This forms a permeable, flexible floor.
The rubber crumb offers cushioning, slip-resistance, noise reduction, and insulation. The resin binds the rubber particles to a long-lasting surface.
Key utility regions encompass driveways, patios, playgrounds, walkways, and pool decks.Compliance and drainage are beneficial properties.
Installation involves proper site prep, mixing and pouring of the rubber resin mixture, compacting to an excellent layer 20mm layer, and curing.
Maintenance includes sweeping, weeding, casting off snow cautiously, and reapplying the resin sealer coat every few years for longevity.
Quality ingredients from official suppliers are essential for surest flexibility, electricity, permeability, and sturdiness.
With the right installation and care, resin-bound rubber crumb can last over twenty years with first-rate performance.
The Main Ingredients of Rubber Crumb surfacing Resin Bound Concrete
There are two primary components in resin-bound rubber crumb surfaces:
Rubber Crumb base
The rubber crumb surfacing consists of granules of recycled tire rubber, sized from 0.5mm to 5mm across. Using recycled tires keeps this waste material out of landfills.
Rubber crumb surfacing top coat is made of 0.2 / 0.5 pigments of rubber in any colour imaginable.
The benifits of rubber crumb are.
Cushioning and shock absorption
Sound dampening
Slip resistance
Thermal insulation
Permeability for drainage
Environmentally friendly
The resin is a clear polyurethane or epoxy coating that binds the rubber pieces together.
The resin provides:
Adhesion for a stable surface
Resistance to UV rays
Permeability for water drainage
Protection from oxidation and weathering
Rubber crumb surfaces can use a polyurethane or epoxy binder. Polyurethane binds well and has more flexibility. Epoxy provides a stronger bond but is more rigid. The resin type should suit the specific application.
How Is Rubber Crumb surfacing Installed?
Installing a rubber crumb surfacing involves preparation, pouring the mixture, and finishing:
Site Preparation
The base should be at least 4 inches thick and compacted for stability.
A porous aggregate is ideal for drainage.
Level and clean the base surface for optimal adhesion.
Mixing and Pouring
Mix the rubber crumb and resin binder to the specified ratio.
Pour the mixture directly onto the prepared base.
Spread and compact it into an even layer.
Finishing the surface consists of.
trowling the surface flat using Polybound releasing agent to stop the rubber sticking to the trowel
Smooth and finish the rubber crumb with a trowel then we roll it with a weighted roller to remove excess rubber and any tough areas to trowel.
Proper subsurface and drainage are key for longevity. Using the right mixing equipment and techniques ensures proper binding. Talk to an installer about the best practices for your specific project.
Key Application Areas for Rubber Crumb surfacing
The beneficial properties of rubber crumb surfacing make it ideal for:
Driveways
Rubber provides flexibility against cracking, rubber is not ideal for vehicle use.
The texture adds skid resistance.
Patios
A softer surface is more comfortable for extended use.
Permeability prevents ponding issues.
Can blend colors for decorative patterns.
Playgrounds
Cushioning provides safety for falls and accidents.
Drainage prevents the buildup of rainwater.
Bright colors and patterns are engaging.
Pathways and Walkways
Flexibility and traction prevent slips and falls.
Permeability allows it to replace concrete and asphalt.
Can match the style of landscaped gardens.
Pool Decks
Provides grip when wet for safety.
A softer feel is easier on bare feet.
Permeability prevents standing water issues.
The compliance, traction, drainage, and aesthetics make rubber crumb surfacing an excellent choice for areas like these that demand specialised performance.
Benefits of Using Rubber Crumb surfacing.
Rubber crumb surfacing: Compared to standard concrete, rubber crumb resin-bound concrete provides many advantages:
Cushioning and Shock Absorption: The rubber granules provide softness and flex underfoot as well as resilience against impacts. This reduces fatigue and makes the surface safer.
Slip Resistance: The coarse texture of the rubber particles creates a grip against shoes and tires, even when wet. This prevents slips and accidents.
Noise Reduction: The rubber dampens noise from walking, playing. This creates a quieter outdoor environment.
Permeability and Drainage: The resin-bound surface allows water to drain through to the base below. This prevents surface ponding issues.
Flexibility and Crack Resistance: The compliance of the rubber allows flexibility against forces and movement. This greatly reduces surface cracks from freeze-thaw cycles.
Attractive and Decorative: Rubber crumbs can be colored and organized into patterns. This permits for appealing driveways, walkways, patios, and pool decks.
Sustainable: Recycling scrap tire rubber reduces landfill waste and and is perfectly safe to use in the base course, it even complies with bba regulations .
These characteristics make rubber crumb surfacing a superb choice for areas needing drainage.
Maintenance Requirements for Rubber Crumb surfacing
While durable, rubber crumb resin-bound concrete requires some periodic maintenance to maximize longevity:
Cleaning: Sweep away particles like leaves or dust. Use soap and water with a stiff brush for harder stains. Avoid petrol or solvents.
Weed Control: Manually remove any weeds in cracks or joints. Weed-killer chemicals could discolor the surface.
Snow Removal: Plow or shovel snow as needed. Use calcium chloride instead of salt to prevent damage.
Resealing: Reapply the resin sealer coat every 2-three years to repair protection against the elements.
Repairs: Small damaged spots can be patched by cleaning and applying a brand-new rubber crumb and resin. Larger areas may require resurfacing.
The proper installation provides the best durability. Avoid using metal shovels or scrapers that could scratch the surface. With periodic upkeep, rubber crumb surfacing can last 20+ years.
Ideal Suppliers of Quality Rubber Crumb and Resin
Choosing quality ingredients is crucial for the best resin-bound rubber crumb concrete surface. Look for:
Rubber Crumb
Sourced from recycled tire rubber
Granules sized from 0.5mm to 5mm
Free of contaminants like metal and cotton
Black or coloured as needed
Consistent size and shape for a smooth finish
Resin Binder
Polyurethane or epoxy options
Low viscosity for binding and permeability
UV-stable for outdoor use
High strength and durability
Standard set time around 2 hours
Reputable suppliers like [polybound ], [Tarmac], and [srb] offer rubber crumbs and resin tested for quality resin-bound surfaces. Consult with them on selecting the right components.
An Ideal Resin Bound Rubber Crumb Recipe
Here is an example recipe for a durable resin-bound rubber crumb concrete surface:
Rubber
Here is an overview of the complete installation process:
Prepare the Base Surface
Dig down at least 4 inches and grade flat
Compact aggregate or porous base layer
Ensure proper drainage slope of 1%
Clean and sweep away all debris
Mix the Rubber Crumb and Resin
Combine as per specified ratios
Mix thoroughly until fully blended
Avoid creating clumps of resin
Pour Out the Mixture
Pour directly onto the prepared base
Spread out over the surface area
Compact and Level
Use a compactor or hand-tamper
Compress to a consistent depth
Grade flat and smooth
Let Cure
Allow to harden initially undisturbed
Curing time varies by temperature
With proper installation, you can achieve a seamless resin-bound rubber surface that will provide lasting performance and enjoyment.
Practical Tips for Working With Resin-Bound Rubber Crumb Concrete
Here are some helpful tips when pouring and finishing resin-bound rubber:
Store materials sealed until mixing to prevent contamination
Use calibrated buckets for precise rubber crumb-to-resin ratios
Mix in small batches that can be poured before the resin sets
Work in cool conditions to slow resin curing time
Pour and spread the mixture across the surface systematically
Compact and smooth the layer thoroughly for the best adhesion
Carry extra rubber crumbs to fill any voids after compacting
When finishing, moisten the trowel with Polybound trowel cleaner to prevent sticking
Wait for the full curing time before allowing any use
Proper planning, preparation, and installation techniques will ensure optimal results. Consider hiring an experienced contractor for best results.
Why Choose Aurora For Your Resin Bound Rubber Crumb Project?
For homeowners in manchester looking to install a rubber crumb surface, we have the skills to complete the project successfully:
Frequently Asked Questions
What thickness should the rubber base be?
The rubber base must have a minimal thickness of four inches for proper balance and strength?
How soon can I use the floor after finished?
What if it rains properly after set up?
How hot does the temperature need to be?
Ideally, the temperature should live above 11c for the correct curing of most resin merchandise.
How long does poured rubber crumb last?
With the right installation rubber crumb surfacing generally last 10 to 25 years.
Conclusion
With its specific blend of recycled substances, compliance, traction, drainage, and aesthetics, resin-bound rubber crumb is a revolutionary and sustainable floor choice. Understanding the components, setup process, programs, advantages, and protection wishes will allow you to properly utilize this material on your next mission.
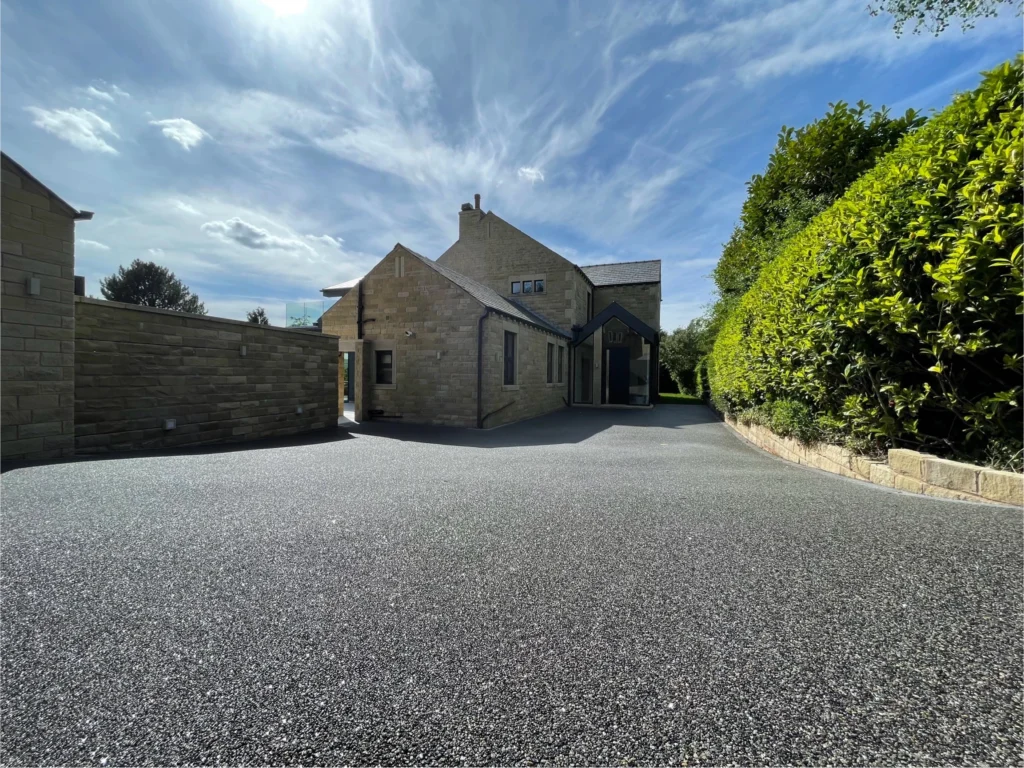
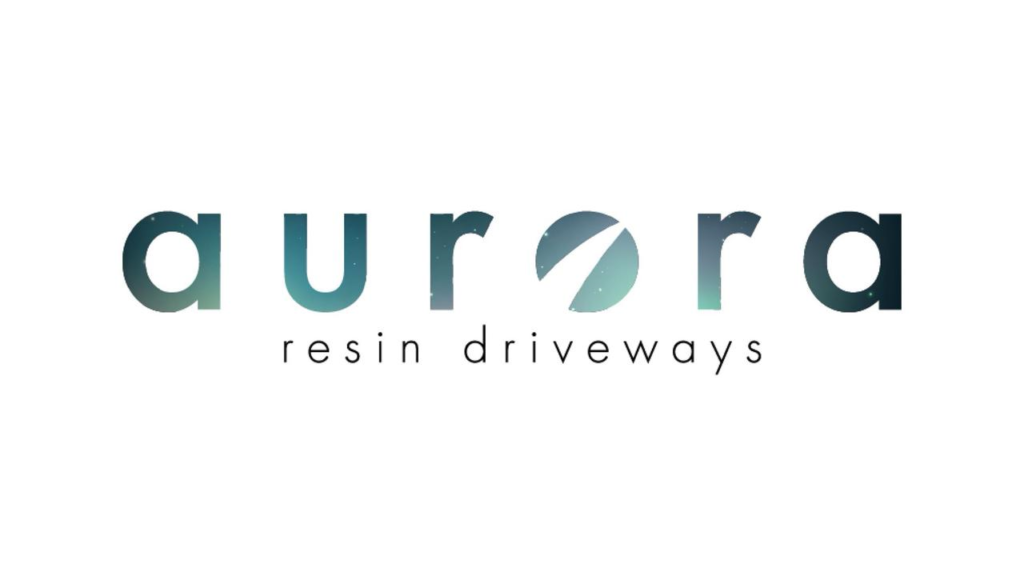